Winding of a transformer
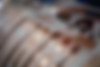
The choice of winding type depends on the transformer specifications, such as voltage, current and power requirement, and on customer preferences.
The transformer windings are made using thin copper tape insulated with quality paper and the layers are applied in order to obtain the specific current density required by the project. In the case of cast resin transformers, the insulating material forms a solid shell around the winding cores, protecting them from moisture and dust particles and providing increased resistance to electrical stress.
Metals commonly used for cast resin transformer windings include copper and aluminum.
- Aluminium transformers have a higher volume but lower mass than copper ones, resulting in slightly larger magnetic core sizes but lower overall weight.
- Aluminium windings offer better short-term over-load capability and similar hot-spot temperatures compared to copper windings.
- The dielectric performance of both materials is considered identical.
- The overall efficiency shows a negligible difference, but for more efficient transformers, aluminium is economically favorable due to lower load losses.
- However, copper transformers are significantly more expensive without significant technical performance variation.
In conclusion, both aluminium and copper windings provide reliable transformers with comparable technical performance. Aluminium windings offer advantages in terms of weight and short-term over-load capability, while copper windings may have a slight advantage in efficiency but come at a higher cost.